Ramsay Pressure Control Valve
Liquid pressure in an agricultural sprayer must be controlled so as to apply the correct volume of spray per hectare.
Most sprayer pumps are positive-displacement pumps driven by the tractors power take off, with higher flow rates than is actually required. Part of the pump’s output is therefore returned to the tank through a bypass line, and spray pressure is controlled by a regulating valve in this by-pass line.
Ordinary regulators can maintain a constant pressure if the volume of liquid does not vary too much. But when it is necessary to shut off part of the spray-boom in order to avoid doublespraying, there is a large increase in the by-pass flow and this causes the pressure to rise unless special compensating valves are fitted and correctly set.
Ramsay pressure-sets automatically maintain constant pressure over a far wider range of variation in flow-rate; for example the by-pass flow through the ‘Nocton’ model can increase from 1 to 100 litres/minute with an increase in pressure of only 0.2 bar. This allows the sprayboom to be shut off with ordinary valves; it also allows the operator to change gear (and so change the pump speed) without affecting the pressure.
Ramsay Pressure-Sets are non-electric, and the only moving part is a flexible diaphragm; the working pressure is set by inflating the pressure-set with air.
It is often desirable to vary the pressure while spraying, either automatically or manually. This can be done by a small electric air compressor and two valves which respectively increase or reduce the air pressure behind the diaphragm; these valves may be actuated by an electronic ground-speed-related system, or controlled manually by the operator.
How it Works
When the pressure in the IN chamber exceeds the air pressure it pushes the diaphragm away from the holes (as shown below) allowing some of the liquid to pass across to the OUT chamber, thus relieving the pressure (A backing plate, not shown in the diagram, prevents the diaphragm from being stretched too far).
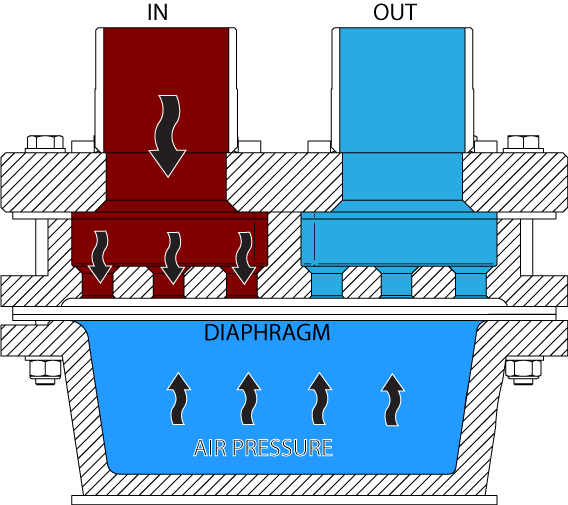
In practice, the diaphragm opens just as far as it needs to for the liquid pressure and the air pressure to come into equilibrium. When a boom is shut off and more flow needs to return to the tank, the diaphragm opens wider and remains in equilibrium in its new position.
Consequently, as long as there are no restrictions in the line back to the tank, the pressure remains constant even when there are large changes in pump speed or spray speed-boom demand, only varying slightly as the compression of the air in the air-reservoir varies with the movement of the diaphragm.
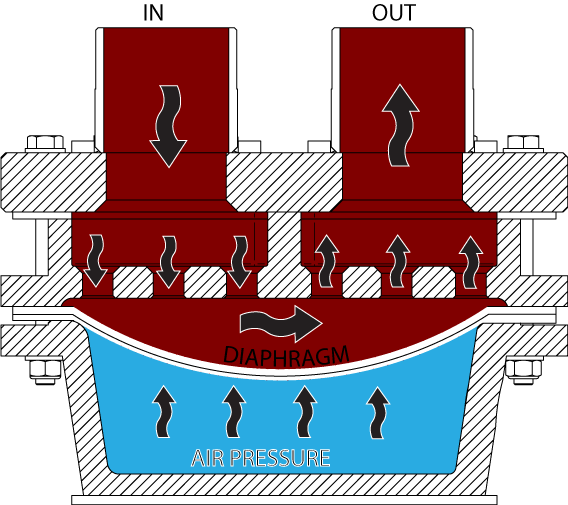